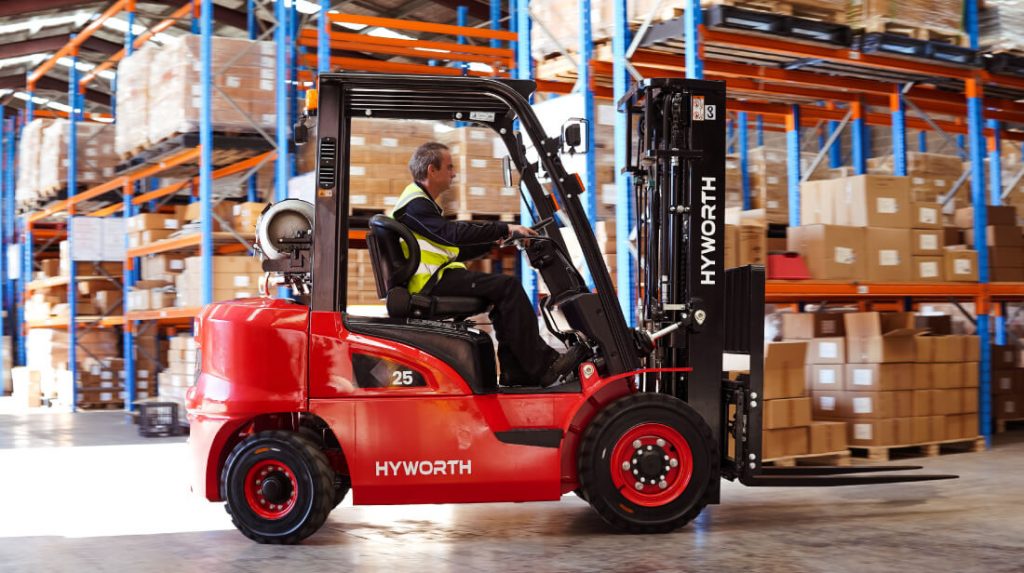
While consumers turn to shopfronts and retail websites for their purchases, what happens at the warehouse is every bit as important in fulfilling their retail therapy. Outside of retail too, the warehouse in any sector is the central hub that must be supremely efficient, super organised and optimally equipped to keep all the cogs turning throughout the supply chain. So how can you ensure that your warehouse is a productivity powerhouse?
No. 1 – Involve your people in productivity strategies
Educating your workforce on the importance of productivity is key. It’s not enough for employees to turn up for work and just get on with the job. Involve them in discussions around meeting productivity KPIs and set targets based on the day or week’s orders or other metrics. Reward achievements and review performance regularly. Ask your employees what would help to increase productivity and implement their suggestions. A workforce that is consulted is a workforce that is more invested in any outcome.
No. 2 – Invest in high-performance equipment for optimal warehouse productivity
Don’t be tempted into purchasing, hiring or leasing inferior equipment and machinery as it will result in a false economy. Breakdowns and downtime are costly and significantly impact on workflow, rostering and output. Often, cheaper equipment is offset by higher running costs and conversely, a sound investment in more efficient equipment will save you money in the long run.
Hyworth Forklifts offer a wide array of forklift solutions to suit all sized businesses, workspaces and material handling needs. We offer a consultancy service for all our clients to determine the best solution to promote optimal warehouse productivity.
No. 3 – Chart the most productive route through your warehouse
Assemble the appropriate members of your workforce to examine the most logical transit of goods through your warehouse. Identify short and long-term storage needs, reposition any high-volume goods to a more efficient location and consider positioning complementary products closer together.
Identifying and implementing the most efficient picking path will save labour hours, prevent staff fatigue, reduce picking errors and increase efficiencies throughout your facility. Additionally, you will be able to isolate the need for heavy equipment usage to areas less frequented by pickers, thus improving health and safety.
No. 4 – Maintain a strict service and replacement schedule for equipment
When your equipment is in full working order, your warehouse’s productivity thrives. Avoid unexpected downtime by maintaining strict protocols including preventative maintenance and scheduled servicing. Assign a manager to oversee the schedule and to report back when any equipment is showing signs of needing to be replaced. Pre-empting equipment failure is important because capital investment is best made when there is ample time to allocate budget and seek advice on the best replacement equipment.
Productivity is profit. No business can afford to perform at anything below full productivity for any length of time.
When it comes time to service or replace your existing forklift inventory, or a single forklift, talk to us at Hyworth Forklifts. We can also assist around solutions to improve your picking routes.