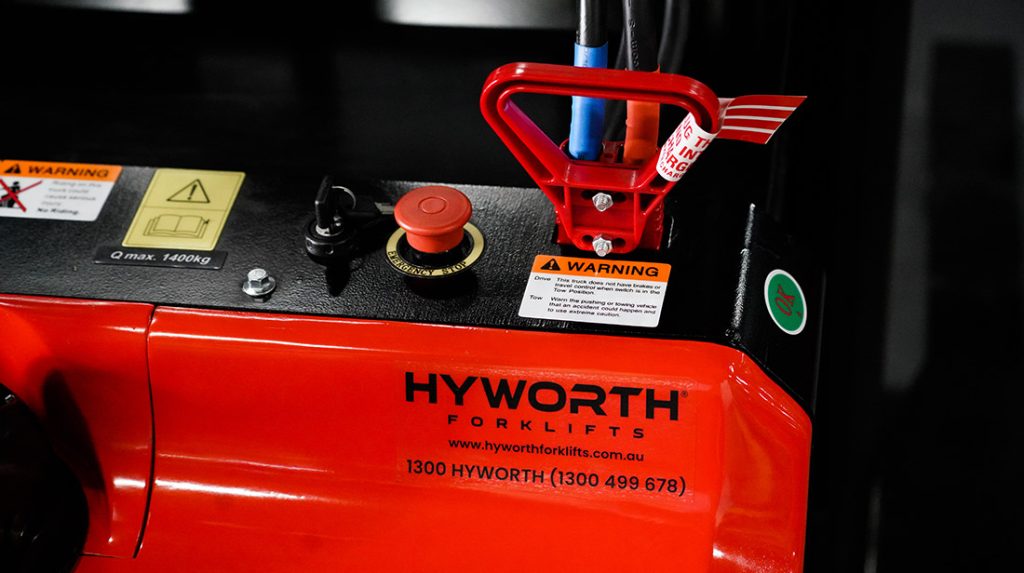
Forklifts are powerful machines commonly used to lift and move heavy loads in workplaces. However, they also present significant forklift hazards if not handled properly. These hazards can lead to serious accidents, injuries, and even fatalities. From improper operation to unsafe environments, the risks are numerous and must be addressed to ensure workplace safety.
Understanding common forklift hazards is essential for reducing these risks. By being aware of potential dangers, businesses can take proactive steps to prevent accidents and create a safer working environment. Proper training, regular maintenance, and adherence to safety guidelines are crucial in mitigating these hazards and protecting both operators and those nearby.
Improper forklift operation
One of the most common forklift hazards is improper operation. When forklifts are driven recklessly, such as speeding, sharp cornering, or sudden stops, the risk of accidents significantly increases. These dangerous behaviours can lead to collisions, tipping over of the unit, or even loss of control, which puts both operators and bystanders at risk.
To avoid these hazards, it’s crucial that all operators undergo proper forklift training. Having a valid forklift certification ensures that operators understand the risks associated with careless driving and are equipped with the skills needed to safely operate the machine.
For example, speeding in a forklift not only reduces the driver’s ability to stop in time but also increases the chance of tipping over. Similarly, sharp turns or carrying loads that are improperly balanced can easily lead to an accident.
By ensuring that forklift operators are trained and certified, businesses can greatly reduce the risks of improper forklift operation and the likelihood of serious forklift accidents. Regular safety checks and supervision can also help prevent dangerous behaviour, keeping both the operators and others in the workplace safe.
Overloading the forklift
Overloading is another major forklift hazard that can lead to serious accidents. Every forklift has a maximum load capacity, and exceeding this limit puts both the operator and the load at risk. When a forklift is overloaded, its stability is compromised, making it more likely to tip over. This can cause significant damage to the forklift, the load, and, most importantly, it endangers the operator and nearby workers.
One of the most common results of overloading is forklift tipping, which occurs when the centre of gravity shifts due to the heavy load. This not only puts the operator in danger but can also lead to severe damage to equipment and goods.
To avoid these risks, it’s crucial that all operators know the load capacity of the forklift they are using. Before lifting any load, check the weight and ensure it does not exceed the forklift’s limit. Additionally, securing the load properly is just as important. Unsecured loads can shift during operation, further increasing the risk of accidents.
Pedestrian hazards in the workplace
One of the biggest forklift hazards in any workplace is the danger posed to pedestrians. Forklifts are large and often operate in areas where people are working nearby, increasing the risk of accidents. If a pedestrian is struck by a moving forklift, it can result in serious injury or even death. Therefore, it’s essential to address pedestrian hazards to ensure a safe working environment.
To reduce these risks, businesses should implement clear safety measures. One effective solution is creating designated walkways for pedestrians, separating them from areas where forklifts are in operation. This helps to minimise the chances of collisions. Additionally, forklifts should be equipped with warning lights and audible alarms to alert pedestrians to their presence, especially when visibility is low.
Clear traffic management plans are also crucial in reducing forklift hazards. These plans should define safe routes for forklifts and pedestrians, reducing the likelihood of accidents. Workers should be regularly trained on these safety procedures to ensure everyone is aware of the risks and how to avoid them.
Forklift maintenance issues
Proper forklift maintenance is essential for preventing dangerous situations in the workplace. A poorly maintained forklift can easily become a serious forklift hazard, leading to accidents that could have been avoided. For example, malfunctioning parts like brakes, alarms, or worn-out tynes can fail at critical moments, causing the operator to lose control of the machine.
When equipment fails, the risks increase significantly. Brakes that don’t work properly can lead to collisions, while faulty alarms may not alert pedestrians or other workers when a forklift is nearby. Worn or damaged tynes also pose a risk as they can drop or mishandle loads, increasing the likelihood of accidents and injuries.
To avoid these problems, businesses should implement a scheduled maintenance program for their forklifts. Regular inspections can catch minor issues before they become major forklift hazards, ensuring that the forklift remains in optimal working condition. Any forklift showing signs of wear or malfunction should be removed from service immediately until repairs are completed.
Environmental and floor conditions
Environmental factors play a significant role, especially when the floor conditions are not ideal. Wet floors, uneven surfaces, and debris in the forklift’s path can easily cause accidents. For instance, a forklift can skid on a slippery surface, or hit a crack in the floor, leading to tipping over. These hazards not only put the operator at risk but can also result in damage to the equipment and loads.
To reduce these risks, it’s important to maintain clean and well-kept floors. Regularly removing debris, fixing cracks, and ensuring the surface is even will create a safer environment for forklift operation. Spills or wet areas should be cleaned up immediately to avoid slips and skids.
Ensuring a safe, hazard-free environment is essential for minimising forklift hazards. By paying attention to the condition of the workspace, businesses can significantly reduce the likelihood of accidents and improve workplace safety for everyone involved.
Blind spots and poor visibility
Forklift blind spots and poor visibility are common forklift hazards that can significantly increase the risk of accidents. When operating a forklift, the driver’s view can be obstructed by the load, creating dangerous blind spots. This makes it difficult to see pedestrians, obstacles, or other vehicles, which increases the chances of collisions.
To reduce these risks, businesses should plan driving routes that minimise the need for sharp turns or manoeuvring in tight spaces. Using spotters is another effective way to guide forklift operators when navigating blind spots, ensuring a safer operation.
Low lighting and adverse weather conditions can also negatively impact visibility, further increasing the risk of accidents. Ensuring the work area is well-lit and providing operators with the appropriate tools to navigate in low visibility can help mitigate these dangers.
By addressing forklift blind spots and improving visibility, companies can significantly reduce the occurrence of accidents and improve overall forklift safety in the workplace.
Hazards related to forklift attachments
Improper or poorly maintained forklift attachments pose serious hazards in the workplace. Attachments, such as clamps or extensions, can alter the forklift’s lift capacity and operating clearances, making the machine more difficult to control. If operators are not trained on how to use these attachments properly, it increases the risk of accidents and equipment failure.
Attachments that are not regularly inspected or maintained can also create safety risks. For example, worn tynes or damaged chains may fail while lifting, leading to dropped loads or loss of control. These forklift hazards can result in injury to the operator or bystanders, as well as damage to goods and the forklift itself.
To reduce these risks, it’s essential to carry out regular equipment maintenance checks on all attachments. Operators should also receive specific training on how to safely use each attachment, ensuring they understand the changes in lift capacity and operation.
Refueling and charging hazards
Refueling and recharging forklifts present serious hazards if not handled carefully. For forklifts powered by LPG or diesel, there’s a fire risk during refueling, especially if safety protocols are not followed. Similarly, forklift charging poses electrocution risks, particularly when batteries are exposed to moisture or poorly maintained.
To reduce these refueling hazards, businesses should create designated refueling areas that are away from sources of ignition, such as open flames or sparks. It’s also essential to ensure these areas have proper ventilation to prevent the buildup of flammable gases.
During battery charging, make sure all equipment is dry and that operators follow proper safety protocols to avoid accidents. Proper training in refueling and charging procedures can greatly reduce the risk of fires and electrocution.
Conclusion
Recognising and addressing forklift hazards is essential for maintaining a safe workplace. By understanding these risks, businesses can take proactive steps to minimise accidents and injuries. Regular operator training, routine maintenance, and strict adherence to forklift safety practices are crucial in reducing potential hazards.
At Hyworth Forklifts, we are committed to helping you improve workplace safety. For expert advice on forklift safety practices or assistance in maintaining your forklifts, contact us today. Together, we can ensure a safer and more efficient working environment.